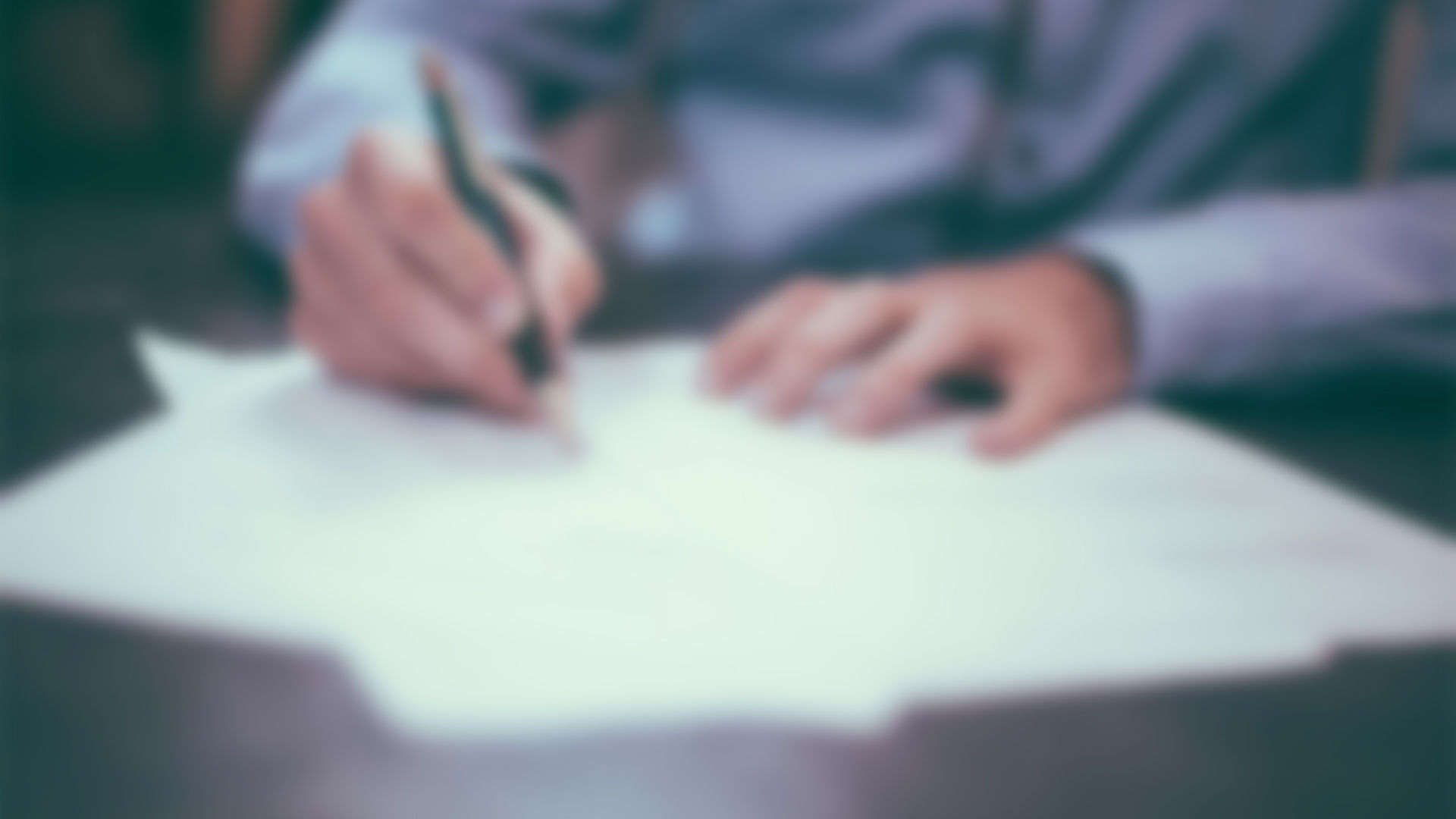
Strategic Consulting Practicum:
CityLab Made In Maryland
Find a business solution that can provide production expansion for raw materials design and international distribution which results in the revitalization of history Jonestown by creating employment opportunity for the underserved community. That describes the challenge in a nutshell. This proposal will not only provide a potential solution but describes an opportunity for Baltimore to become a hub for extending production and distribution for all of MD and the surrounding region. Amazon is a technology company that happens to do retail; Uber is a technology company that happens to offer taxi services; and Airbnb is a technology company rents rooms and houses. These innovative companies didn’t create the best physical product, they created disruption through technology and the idea to do something differently. Platform’s that aren’t product dependent but excel at offering a service level that an industry failed to provide. The business solution described within this proposal does just that -- offer a service level that will exceed customer expectations while setting a new bar for the high-end raw materials design industry.
Requirements/Assumptions:
-
Business solution to scale production for local & regional designers of raw material
-
Have the ability to produce and distribute; missing designs
-
27 vacant lots in Jonestown
-
Goal to create jobs for the local community
Recommendation:
-
Design to Production Platform (DPP) -- Digital platform to facilitate order management, production manufacturing and warehouse management, distribution management, and consumer communication management.
-
DPP will leverage open source technology to create a service oriented architecture.
-
The platform is a product with several layers: Consumer facing UI, CAD consumption and customization configuration, product information management, distributed production model, network dropship interface, distribution interface, consumer communication interface.
-
Benefits:
-
Customizable Designs that are made to order (MTO)
-
Custom products shipped within a week of order
-
Just-In-Time (JIT) Inventory Management
-
Shared shipping rate for domestic and international shipments
Jobs:
-
Software Engineers
-
Quality Engineers
-
DevOps
-
Software Architects
-
Technical Managers
-
Business Analysts
-
Project Managers
-
Customer Service Representatives
-
IT Support
-
Production Training
-
Production Facilitators
-
Warehouse Distribution
​
Business Solution
Developing the DPP will create an opportunity to service any type of raw material production based on four basic concepts: design, component creation, product assembly, product distribution. Our recommendation is to start with wood furniture. Narrowing the scope to one type of raw material development will help the initial system design to be focused and limited to minimum viable product for speed to market.
Current websites for custom wood furniture allow customers to describe the design and custom changes but the product process is very manual. DPP is comprised of a collection of integrated systems (listed below) that allow orders to flow through each subsystem from when the product is configured and ordered through production to distribution.
Design
Designs will be uploaded and managed within the DPP. Configuration details will be identified and made available through a UI for customers to select from a list of options for each component that can be configured.
Component Creation
The platform expects each design to have components that are assembled to create the finished product. A Product Manufacturing System (PMS) within the platform is used to create and configure stations at production facilities. As orders are placed, a queue for the products is created and component creation requests are sent to stations based on station capabilities, current station queue and station average velocity. This allows for simultaneous creation of components that are sent to a holding area once they are complete. PMS tracks incoming orders, the production queue, and future forecasting to proactively identify potential bottlenecks in the process.
Product Assembly
Once all the components to build a product is available in the holding area, the PMS will send the components to a product assembly area. Assembly requires individuals operating in this area to have attention to detail and quality. They will be responsible for rejecting components that don’t meet expectations visually and functionally. These individuals are responsible for adding the final touch on each piece of furniture prior to packaging for distribution.
Product Distribution
Finished products are wrapped and package for protection and placed in a holding area until the entire order is available to be shipped. We want to avoid split shipment to keep distribution cost from decreasing margin but they can occur based on product type.
DPP Subsystems
Order Management System
The Order Management System (OMS) manages the processing of orders place through multiple channels (website, phone, 3P), forecasting, purchasing, inventory, financial reporting and data used by customer service tools.
Production Manufacturing System / Warehouse Management System
The Production Manufacturing System (PMS) manages the queue and distribution of component creation and production assembly. The system requires every detail of a design including the specifications for each configurable component. Which can be leveraged through an API where it can be cached and used by consumer facing interfaces at runtime.
Distribution Management System
The Distribution Management System (DMS) tracks the measurements of what needs to be distributed, when it’s available to be distributed, how the orders should be shipped, and contracts the company that will be facilitating distribution. The DMS not only integrates with distribution vendors to inform them when orders are ready for pick up, it will also frequently pull tracking information for proactive communication with consumers.
Customer Relationship Management System
The Customer Relationship Management System (CRM) is the central hub for all customer communication. This system will facilitate transactional communication through email, push notifications, live chat and phone calls.
​
Production Location
DPP will allow for production and assembly to take place across multiple locations. This will allow for the business to expand operations throughout Jonestown to areas that fall within business zoning.